> Read the Press Release version here
Silicon (Si) has been defined as a critical raw material (CRM) by the European Union since 2014, due to its high supply risk and economic importance. Si has high economic importance in the EU due to its irreplaceable presence in numerous products on which our society relies.
The demand for silicon in solar applications has experienced rapid growth during the past decade.
At the moment, the production of Silicon and solar panels represents a carbon and energy-intensive process, which produces several low-value byproducts and wastes. Thus, a shift away from waste generation and carbon emissions towards circularity is necessary for creating a sustainable industry.
In recent months, partners of the Resilex project have worked hard to test a new way for the production of silicon.
The new process developed consists of carbon-free, sustainable, aluminothermic reduction of molten silicates (oxide melts) by aluminum scrap. This will be tuned and optimized for the production of pure Si suitable for solar energy and battery applications and.
What are the ingredients?
During the sawing of silicon ingots into very thin slices, utilizing a diamond wire, roughly 40% of the material is lost as micro parts of silicon. This waste is flushed away by a sawing liquid creating a sludge. The crystalized sludge is called “kerf” and is composed of ultra-pure silicon.
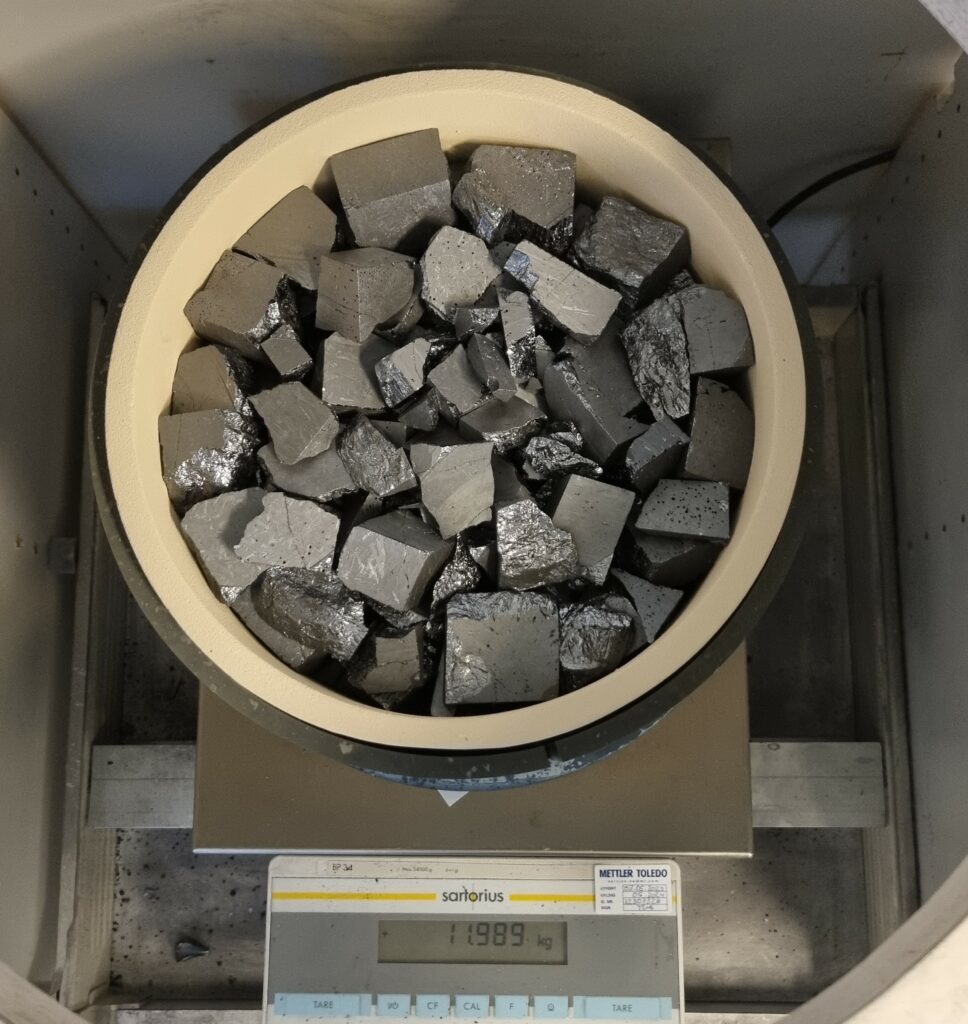
During the silicon refining and smelting, a residue is left over, taking the name of “slag”. Despite being a residue, it still contains a considerable silicon content.
Slag, Kerf, Quartz and a Silicon alloy obtained by aluminothermic reduction of molten silicates (oxide melts) by aluminum scrap or dross are inserted in the furnace for smelting. Once the process is terminated and the slag is removed, the Silicon obtained showed a 98,91% rate of purity.
At NTNU (Norwegian University of Science and Technology), research on techniques for further purification of the acquired product was also conducted. By directional solidification of Si, a refining method based on the distribution of impurities between solid and liquid metal, a purity of 99.86% was achieved.
In the figure: Silicon produced out of waste materials and prepared for purification experiment
What to do next
In the following months, the Resilex partner CEA will carry out further tests to evaluate the suitability of the waste material for the production of solar cells and Li-on batteries. This will be a major step forward in making the European value chain more circular and sustainable.
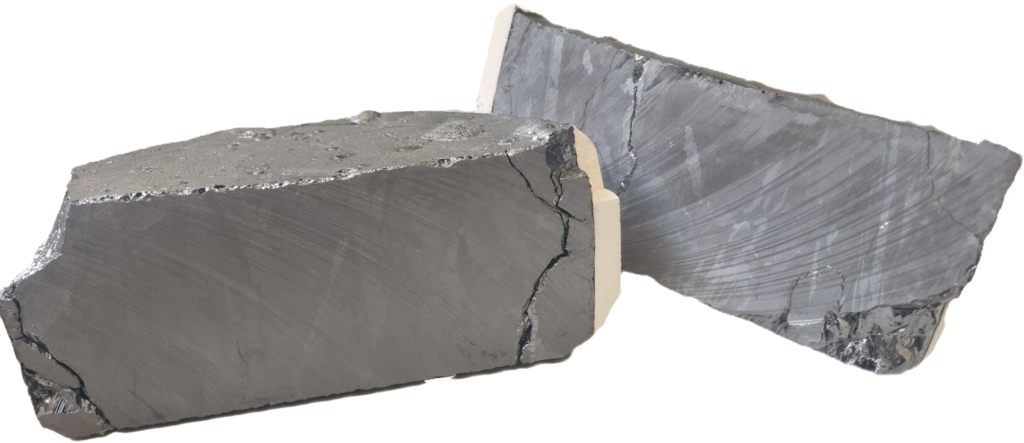
Silicon ingot made by directional solidification of silicon produced out of waste materials